Overview: The TALOS base layer was an endeavor in wearable technology, focused on developing a sensor-equipped suit for comprehensive biometric monitoring, including EMG, ECG, and EEG. This project represented a significant leap forward in combining advanced textile engineering with cutting-edge electronics to create a wearable that was both functional and ergonomic while seamlessly blending with a full military exoskeleton.
Role and Responsibilities
Role: Assistant Textile Engineer
Responsibilities: I played a key role in the integration of electronic sensors within textile substrates. My responsibilities also included aiding material fabrication processes and ensuring that the design configurations were optimized for both functionality and wearability.
Role: Assistant Textile Engineer
Responsibilities: I played a key role in the integration of electronic sensors within textile substrates. My responsibilities also included aiding material fabrication processes and ensuring that the design configurations were optimized for both functionality and wearability.
Technical Details and Innovation
Materials Used:
Materials Used:
Thermoplastic Polyurethane (TPU): Chosen for its elasticity, durability, and strong bonding capabilities with conductive materials, TPU was essential for embedding the suit with sensors without affecting the mobility of the person wearing it.
Silver-Printed Traces: These conductive traces were printed on the TPU film to facilitate electrical connections between the sensors, ensuring reliable transmission of physiological data.
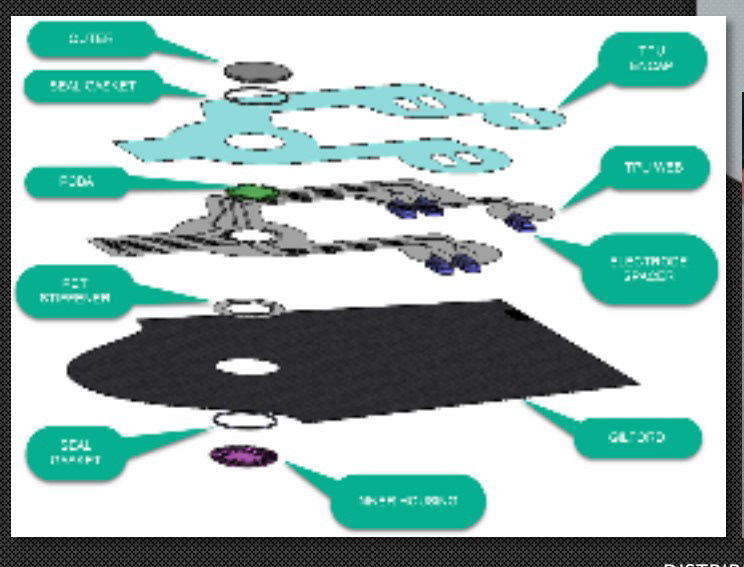
Sewing and Assembly Techniques:
Advanced Sewing Machines: I used both flatbed and cover-stitch sewing machines to piece together the sensor suit with a very high level of accuracy and durability. These machines could provide strong, resilient stitching which could bear the physical strain from everyday wear and tear while staying intact to protect the embedded electronics.
Heat Bonding: Used to bind layers of fabric together and hold the electronics in place, allowing them to remain functional over the whole life cycle of the garment. This process was carefully controlled to avoid any kind of damage to the sensitive components.
Laser Cutting: Necessary for adhering to the tolerances needed for accurate component fit and reliable function of the conductive materials. Laser cutting allowed for the intricate pattern work necessary for sensor placement and integration.
Optitex 3D CAD Software:
Custom Fit Design: Optitex was leveraged to create suits tailored to two individual users through 3D body scans, ensuring a perfect fit that maximized sensor efficacy and wearer comfort.
Material Simulation: The software’s simulation capabilities allowed us to predict how different fabrics and designs would act on the body. With this one can adjust the design before the prototyping phase, ultimately saving resources and time.
Importing Material Properties: The ability to import specific fabric properties, such as stretchability, thickness, and weight, was instrumental in accurately modeling the suit’s behavior under different conditions.
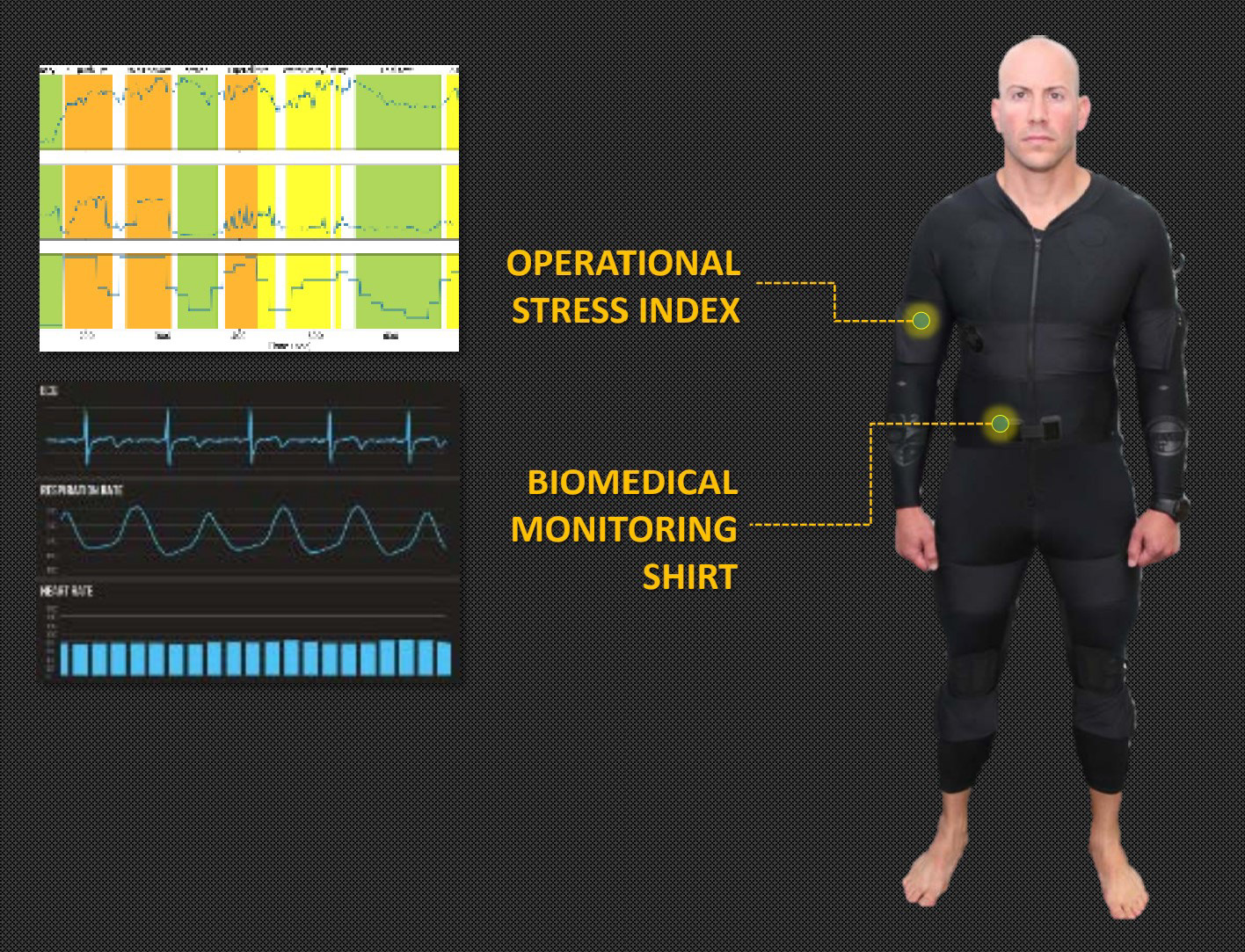
Challenges Overcome:
Signal Integrity: We addressed challenges related to electrical noise and signal degradation caused by the integration of multiple sensors and conductive paths within a flexible, wearable format.
Durability: A key focus was ensuring that the suit could endure strenuous wear and tear, including stretching and moisture, without compromising the functionality of the embedded sensors.
Outcome and Impact:
The project resulted in a small prototype run of two sizes that successfully demonstrated the feasibility of integrating extensive biometric monitoring capabilities into a wearable suit.
The project resulted in a small prototype run of two sizes that successfully demonstrated the feasibility of integrating extensive biometric monitoring capabilities into a wearable suit.
Reflections and Learnings:
Throughout the project, we overcame various setbacks related to sensor integration and material failures. These challenges reinforced the importance of resilience and adaptability in research and development. As this was my first time working closely with experts in electronics, textile manufacturing, and software development, the process highlighted the necessity of being able to communicate across disciplines while leveraging diverse skill sets for solving complex problems.
Throughout the project, we overcame various setbacks related to sensor integration and material failures. These challenges reinforced the importance of resilience and adaptability in research and development. As this was my first time working closely with experts in electronics, textile manufacturing, and software development, the process highlighted the necessity of being able to communicate across disciplines while leveraging diverse skill sets for solving complex problems.
Links: